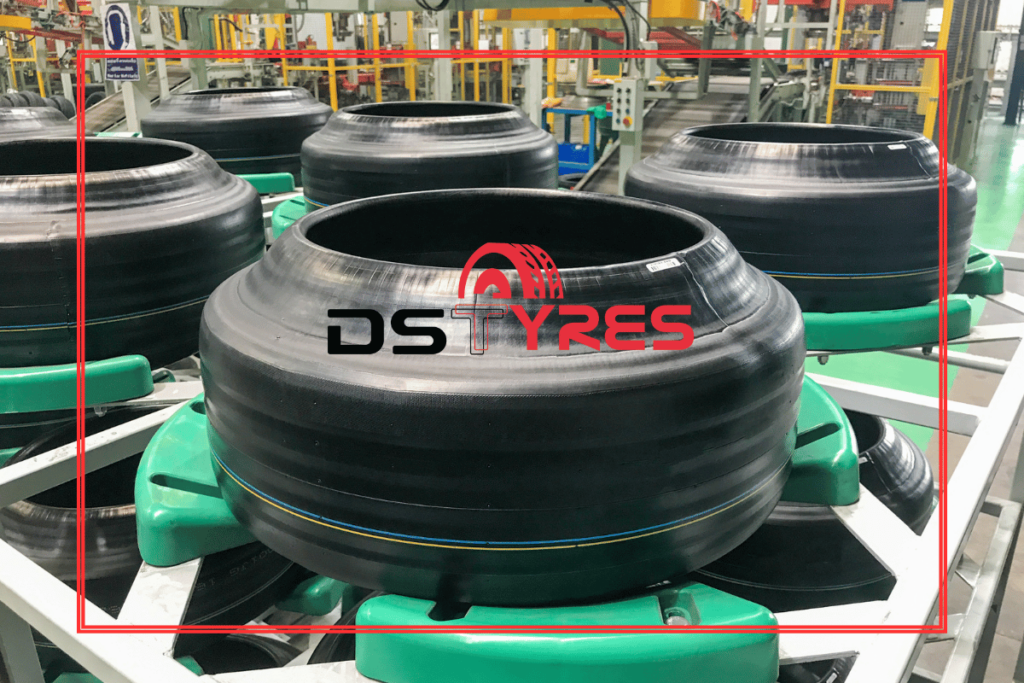
- Introduzione
- La Struttura e la Composizione di un Pneumatico Moderno
- La Mescola di un Pneumatico: Un Equilibrio di Scienza e Arte
- La Creazione della Carcassa e l'Assemblaggio dello Pneumatico
- Processo di Cottura e Vulcanizzazione
- Valvole e Protuberanze
- Controllo Qualità: La selezione all'ingresso
- Conclusione
Introduzione
Un pneumatico è ben più di un semplice cerchio di gomma. È una complessa unione di scienza, ingegneria e tecnologia che ha cambiato radicalmente il modo in cui ci muoviamo nel mondo. L’evoluzione degli pneumatici ha avuto un impatto immenso non solo sul settore dei trasporti, ma anche sull’intero corso della mobilità umana.
Durante gran parte della nostra storia, l’uomo ha viaggiato su ruote fatte di legno e metallo. Tuttavia, con l’invenzione degli pneumatici gonfiabili all’inizio del ventesimo secolo, è iniziata una nuova era nel settore dei trasporti. Questa rivoluzione ha reso i viaggi più confortevoli, sicuri ed efficienti, e ha dato vita a una vasta industria dedicata all’innovazione e alla produzione.
Gli pneumatici moderni sono il risultato di un lungo processo di ricerca e sviluppo, e ogni pneumatico è costituito da oltre 15 diversi elementi, tra cui gomma naturale e sintetica, additivi chimici e nero di carbone come pigmento. Ma come si passa da questi materiali grezzi a un pneumatico finito, pronto a percorrere migliaia di chilometri sulle strade? In questo articolo, vi guideremo attraverso i processi di produzione, le tecniche e le tecnologie che rendono possibili gli pneumatici che usiamo ogni giorno.
La scoperta di questo mondo affascinante dimostra quanto sia complesso un oggetto che diamo spesso per scontato. È una storia che parla di innovazione continua, di progresso tecnologico e di un oggetto che è parte integrante della nostra vita quotidiana. Unisciti a noi in questo affascinante viaggio alla scoperta di come è fatto un pneumatico, e preparati a vedere questo oggetto familiare sotto una luce completamente nuova.
La Struttura e la Composizione di un Pneumatico Moderno
Un pneumatico moderno è una meraviglia dell’ingegneria e della chimica, combinando vari materiali e processi per creare un prodotto che è al contempo resistente e flessibile. Comprendere la struttura e la composizione di un pneumatico moderno significa esplorare una serie di componenti interconnessi che lavorano insieme per fornire prestazioni ottimali.
In primo luogo, la materia prima. Gli pneumatici sono composti principalmente da gomma naturale e sintetica. La gomma naturale offre elasticità e flessibilità, mentre la gomma sintetica aggiunge resistenza e durabilità. Queste due tipologie di gomma vengono combinate con additivi chimici e pigmenti, come il nero di carbone, che conferisce al pneumatico il suo colore distintivo e aumenta ulteriormente la resistenza.
Il battistrada è la parte dello pneumatico che entra in contatto con la strada. È progettato per fornire aderenza e stabilità, e può avere diverse formule a seconda delle esigenze di prestazione. La combinazione di gomma, silice e altri materiali nel battistrada aiuta a migliorare l’aderenza su strade bagnate o asciutte e contribuisce a ridurre l’usura.
All’interno dello pneumatico, troviamo la carcassa, costituita da strati di tela gommata che conferiscono allo pneumatico la sua forma e struttura. Questa tela, spesso realizzata in poliestere o altri materiali sintetici, è rivestita di gomma e lavorata per garantire che sia abbastanza rigida da mantenere la forma del pneumatico, ma anche flessibile da assorbire gli urti della strada.
Il tallone è una parte cruciale dello pneumatico, costituita da fili di acciaio intrecciati che assicurano che lo pneumatico rimanga saldamente ancorato al cerchio. Senza un tallone solido, il pneumatico potrebbe staccarsi, causando potenziali pericoli.
Ogni uno di questi componenti è assemblato attraverso un processo meticoloso che utilizza macchinari avanzati e tecnologie all’avanguardia. Dalla calandra che applica la gomma calda sui fogli di poliestere alla macchina che intreccia i fili di acciaio per il tallone, ogni passaggio è calibrato per garantire un pneumatico di alta qualità.
La Mescola di un Pneumatico: Un Equilibrio di Scienza e Arte
Costruire uno pneumatico è un processo che assomiglia straordinariamente all’arte della cucina di alta classe. Come un cuoco stellato prepara una ricetta con ingredienti precisi e tecniche raffinate, così un pneumatico viene creato combinando oltre 200 ingredienti in proporzioni e modalità esatte. L’atto di mescolare questi componenti è un delicato equilibrio di scienza e arte che richiede una precisione e maestria estrema.
Gli ingredienti principali in questo “piatto” tecnico sono quattro:
- Gomme o Elastomeri: Possono essere sia naturali, estratte dall’albero della gomma, sia sintetiche. Sono la base della mescola, conferendo elasticità e resistenza.
- Cariche Rinforzanti: Questi includono il nero di carbonio, che dà ai pneumatici la loro colorazione nera, e la silice, che riduce la resistenza al rotolamento. Servono a rafforzare la struttura dello pneumatico.
- Plastificanti: Solitamente oli o resine, sono fondamentali per amalgamare e omogeneizzare la mescola, facilitando anche l’estrusione.
- Additivi Chimici: Presenti in granuli o polveri, questi componenti sono spesso complessi nella loro formulazione e dosaggio. Lo zolfo è uno degli additivi chiave, essenziale per il processo di vulcanizzazione.
Gli ingredienti vengono prima frantumati, poi misurati e mescolati con una precisione rigorosa. La formulazione richiede una conoscenza approfondita della chimica e della fisica, così come una comprensione delle proprietà desiderate dello pneumatico finale. La temperatura e il modo di “cucinare” questi ingredienti sono tanto cruciali quanto le proporzioni stesse.
La mescola risultante è una sostanza unica, creata per specifiche caratteristiche in termini di aderenza, flessibilità e durata. Ogni formulazione di mescola è diversa dall’altra, riflettendo la vasta gamma di esigenze e applicazioni per cui gli pneumatici vengono utilizzati.
Da questa mescola, vengono quindi realizzati diversi componenti come carcasse, profilati, cerchietti e semiprofilati, ciascuno con una funzione specifica nella costruzione dello pneumatico.
La Creazione della Carcassa e l’Assemblaggio dello Pneumatico
Entrare nello stabilimento di produzione pneumatici è come entrare in un mondo automatizzato e altamente specializzato. La Linea MAC (Macchina Automatica di Confezionamento) è il cuore pulsante del processo, composta da 23 stazioni che combinano i diversi elementi dello pneumatico in modo completamente automatizzato.
- Il Tamburo: Tutto inizia con un tamburo su cui vengono adagiati, passo dopo passo, i diversi elementi. È un processo altamente preciso che crea lo scheletro dello pneumatico.
- Elemento Impermeabile: La prima parte ad essere posata è un sottile strato di gomma impermeabile all’aria, che sostituisce la funzione della camera d’aria.
- Carcassa Radiale: Successivamente, viene sistemata la carcassa radiale, una tela tessile rivestita di gomma con cavi di rinforzo in poliestere. Disposti ortogonalmente al senso di rotolamento, conferiscono resistenza allo pneumatico.
- Bandi di Contenimento e Cerchietto Metallico: La macchina applica quindi le bande di contenimento del cerchietto metallico, un elemento chiave che darà forma allo pneumatico.
- Fianchi della Gomma: Vengono uniti altri due strati di gomma morbida che formeranno i fianchi dello pneumatico, su cui verranno impresse le scritte e le misure.
- Fase di Finizione: Qui la carcassa inizia a prendere forma. Aria e movimento meccanico modellano la struttura, mentre vengono aggiunti due strati di tele metalliche per rigidità e stabilità.
- Tessuto in Nylon e Aramide: Un rivestimento essenziale che resiste alla forza centrifuga alle alte velocità.
- Profilato e Battistrada: L’ultimo elemento è il profilato, che diventerà il battistrada, la parte dello pneumatico a contatto con il suolo.
Questo intricato processo richiede un’attenzione estrema ai dettagli e una perfetta sincronizzazione tra tutte le componenti. Ogni elemento è essenziale, dalla parte più interna impermeabile all’aria al tessuto di rinforzo che garantisce la rigidità.
Processo di Cottura e Vulcanizzazione
Le nostre gomme attraversano un percorso di oltre 30 km su nastri trasportatori all’interno dello stabilimento. Questo tragitto esteso e altamente automatizzato culmina quando le gomme giungono a un punto dove dei robot ad alta precisione si incaricano di spostarle nella fase successiva. È affascinante notare come questi macchinari siano dotati di sistemi di sicurezza che avvisano quando un ostacolo intralcia il loro percorso.
Ora, però, entriamo in una fase cruciale del processo: la cottura. Simile a come un cuoco cuoce un piatto per dargli sapore e consistenza, anche gli pneumatici necessitano di un processo di “cottura”. Questo non avviene in una cucina, ma piuttosto utilizzando una pressa di cottura specializzata, come quella che vediamo ora.
Questa macchina possiede una membrana interna che, riempiendosi di vapore ad alta pressione, spinge il pneumatico contro uno stampo. Questo stampo non solo modella la superficie di contatto dello pneumatico, ma anche le sue parti laterali, dove vengono impressi dettagli come loghi, dimensioni e altre informazioni.
Ma la funzione principale di questa pressa non è solo modellare lo pneumatico. Si tratta di un processo chiamato vulcanizzazione. La gomma viene riscaldata a temperature vicine ai 200 gradi per circa dieci minuti. Questo processo termico causa una reazione chimica nello zolfo contenuto nella gomma, formando nuovi legami tra le molecole. Ciò trasforma la gomma da uno stato plastico a uno elastico. Questa trasformazione è essenziale: senza di essa, lo pneumatico non avrebbe la capacità di tornare alla sua forma originale dopo essere stato deformato, come quando si incontra un ostacolo.
Le moderne presse utilizzate per la vulcanizzazione rappresentano la fine dell’evoluzione tecnologica. Un tempo, il calore necessario era fornito dal vapore, il che causava una perdita di energia ogni volta che lo stampo veniva aperto. Oggi, con l’avvento delle presse elettriche, c’è stato un notevole risparmio energetico, che si traduce anche in una significativa riduzione delle emissioni di CO2: ben 4000 tonnellate in un anno. Un passo avanti notevole sia per la tecnologia che per l’ambiente.
Valvole e Protuberanze
Il processo di finitura degli pneumatici è affascinante e complesso. Dopo essere stati cotti e vulcanizzati, gli pneumatici devono essere raffreddati. Durante questo raffreddamento, il processo di vulcanizzazione continua e solidifica ulteriormente la gomma, rendendola pronta per l’uso.
Un dettaglio interessante riguarda l’eliminazione delle sacche d’aria all’interno dello stampo durante la pressione. Un tempo, questo causava la formazione di piccoli “peduncoli” noti come “tettine”. Queste protuberanze si formavano dove i fori di sfiato permettevano all’aria di fuggire.
Nei pneumatici moderni, questo processo è stato reso più efficiente. Invece di usare i fori che lasciano segni visibili sul pneumatico, si utilizzano valvole specifiche. Queste valvole, che possono variare da 1.500 a 6.000 a seconda dello stampo, permettono l’evacuazione dell’aria senza lasciare segni evidenti.
Controllo Qualità: La selezione all’ingresso
Tutte le gomme che vengono prodotte, e quando dico tutte intendo tutte, tutte. Cioè tutti 14 milioni di pneumatici che ogni anno vengono fatti qui in Italia vengono sottoposti a un controllo qualità. Prima di tutto si va a verificare l’aspetto dello pneumatico, e lo si fa manualmente attraverso una serie di operai altamente specializzati che vanno alla ricerca di ogni minima imperfezione, e non gli scappa niente, vedere lavorare è impressionante. Per fortuna però da alcuni anni questi operatori sono affiancati anche dalla tecnologia. C’è una macchina che si chiama Iris che sfrutta l’intelligenza artificiale per andare alla ricerca di ogni minimo difetto.
Le gomme difettate ovviamente vengono scartate, ma non è finita perché si va a controllare anche l’uniformità, cioè come la gomma si comporta una volta che inizia a girare. Si simula quindi il funzionamento dello pneumatico attraverso questo macchinario ad alta complessità, si montano due semicerchi e la ruota inizia a girare attraverso un volano, poi si raccolgono tutta una serie di dati sul suo comportamento. Ci sono delle tolleranze, ovviamente la gomma si deve deformare entro i valori prestabiliti, altrimenti c’è qualcosa che non va. Questo secondo controllo, ancora più sofisticato, lo si fa su tutte le gomme OEM (di primo equipaggiamento) che vanno direttamente ai costruttori, e a campione su tutti gli altri pneumatici.
Conclusione
La produzione di pneumatici è un processo affascinante e complesso che richiede precisione, competenza e innovazione continua. Dal viaggio iniziale della gomma attraverso i meccanismi altamente automatizzati, fino alla cottura e alla vulcanizzazione, ogni fase è fondamentale per garantire la qualità e le prestazioni del prodotto finale.
L’attenzione ai dettagli, come evidenziato nelle fasi di valvole e Protuberanze, dimostra quanto sia critico il controllo del processo per evitare imperfezioni e garantire l’efficacia di un pneumatico sicuro. Inoltre, il controllo qualità è una tappa obbligatoria, dove l’uso di tecnologie avanzate, come l’intelligenza artificiale, si affianca all’esperienza degli operatori per individuare ogni minima imperfezione.
Questa sinergia tra uomo e macchina sottolinea l’importanza di un equilibrio tra la tradizione manifatturiera e l’innovazione tecnologica. La combinazione di metodi tradizionali con soluzioni all’avanguardia consente di produrre pneumatici sicuri ed efficienti, rispettando al contempo l’ambiente attraverso l’adozione di processi sostenibili.
Infine, è fondamentale riconoscere che dietro ogni pneumatico c’è una rete di professionisti dedicati, macchinari sofisticati e un impegno incessante verso l’eccellenza. Il risultato è un prodotto che non è solo un componente necessario per il nostro trasporto quotidiano, ma una testimonianza dell’ingegneria, della chimica e della dedizione all’arte della produzione. La storia raccontata attraverso queste pagine svela un mondo che va oltre la semplice ruota, trasformando la gomma in un simbolo di progresso, innovazione e qualità.